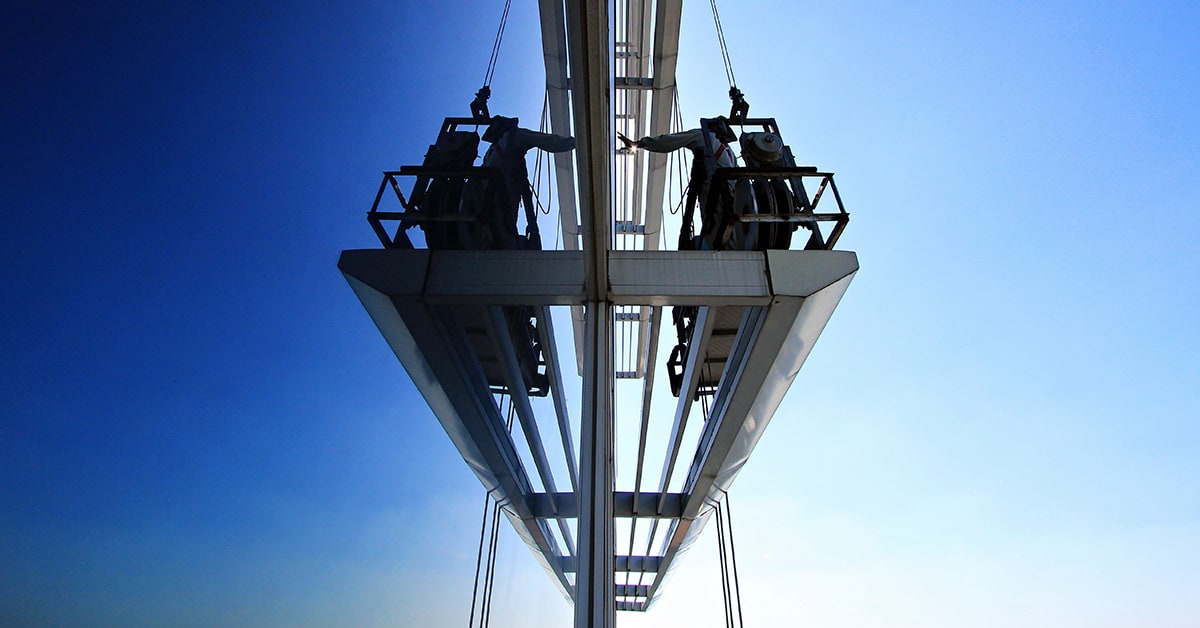
.
This is the fifth in a series on the relevance of Operations & Maintenance (O&M) in architecture. In preceding posts, we explored the broad reasoning behind building maintenance, the three principle approaches, cost-effective means of implementation , and the importance of the building envelope. Here in part 5, we look at how maintenance provisions need to be considered practically and the consequences of not doing so.
Maintenance—or rather, the lack of it—is often the cause of failures that occur during the service life of a building. Very few maintenance-related failures stem from the improper application of repair methods or materials. Instead, problems typically begin when prescribed maintenance is deferred or not carried out for reasons of cost, safety, or unavailability of proper equipment or expertise. The logic of such “deferred maintenance,” may be self-defeating. Sometimes, however, there are good reasons why maintenance does not or cannot happen. These include limitations in the availability of specialized equipment, access to skilled labor, or the viability of the prescribed processes.
Though architecture is a globalized profession where ideas flow freely across borders, it cannot be assumed that any given design concept, building form, or construction technology will perform equally well in different contexts. For example, it’s no surprise that a building in Brasilia has different needs than one in Riyadh. This principle applies to maintenance systems as well. The exterior envelope, to name only the most obvious area, requires ready, practical, and affordable access for cleaning, inspection, maintenance, and repair. If provision for these activities is not incorporated into the building’s envelope during the design process and factored into the associated cost plan, the consequences may be both expensive to the owner and jarring to the finished form of the building.
How will a lightbulb be changed in the ceiling of a ten-story atrium? How will a chiller unit installed behind a complex louvered wall be serviced for maintenance or replacement? These and countless other maintenance considerations underscore the need to plan for convenient access to all building systems. To fulfill and extend a building’s expected service life, architects and owners must think practically. How will rooftop air handling units be replaced in a deep-plan building that is set back far from a road? How will a curtain wall be cleaned on an irregularly shaped 60-story tower in a dense urban context? It is worth resolving such maintenance-related quandaries in advance of construction, if possible.
For each of the above examples, the necessary maintenance equipment may be available in major cities, but in smaller, more remote locations, it may not be available or may be prohibitively costly to bring to the site. Improvised alternatives might be unsafe, jeopardizing worker safety and potentially exposing owners to legal liability.
Ideally, the means of maintenance access will be designed into the building facade or roof from the start, based on service life expectations and the concomitant maintenance and inspection needs. When the local availability of equipment necessary for predictable maintenance tasks is in question, owners of larger facilities may consider purchasing such equipment to ensure smooth maintenance and lower associated risks.
This integrative approach to maintenance design will be the subject of the sixth and final part of this series about the art of maintenance.
Omrania, a renowned architecture firm, has established a reputation for excellence in blending aesthetic and functional design, setting a benchmark for architecture firms in Riyadh, Saudi Arabia.