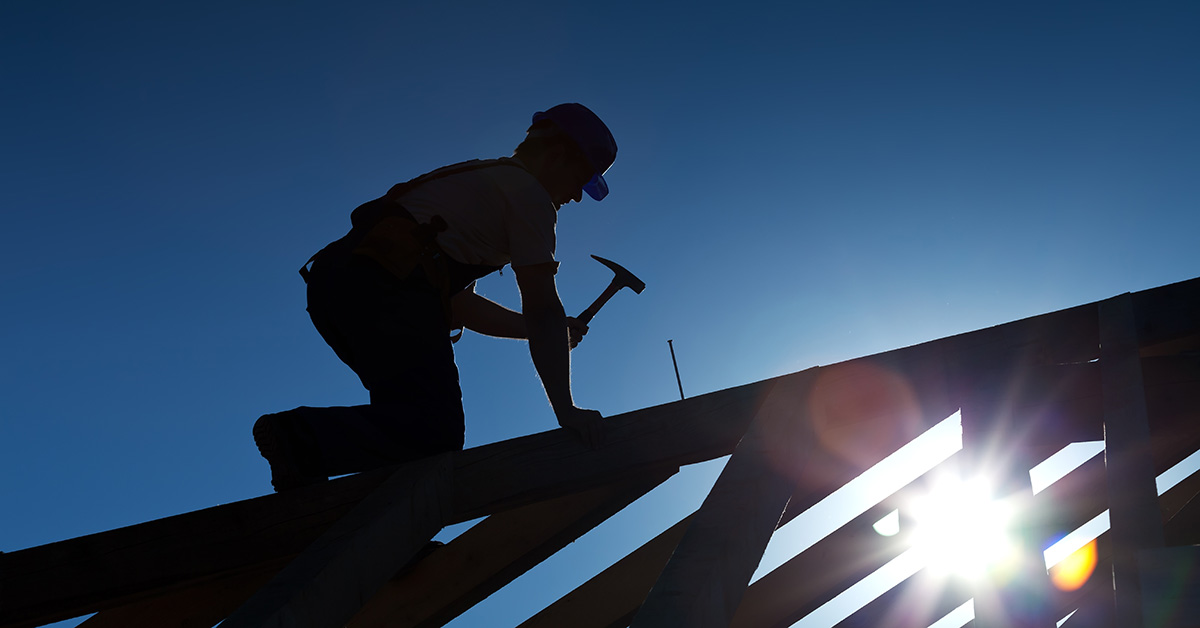
.
In preceding posts, we explored the broad reasoning behind building O&M and the three principal approaches. In part 3, we map out practical implementation of O&M plans.
Deferred building maintenance is a worrying trend because the cost can be as much as 30 times that of early intervention. With budgets squeezed, it may be tempting to ignore this risk and reduce or even eliminate maintenance budgets for the sake of short-term cost savings. But the recommended preventative maintenance budget of 2% to 6% of an annual operating budget quickly balloons into a formidable sum if deferred for even just a few years.
Think of a proactive O&M approach as preventative medicine for a building. The problem with ignoring it is that minor repairs quickly become major replacements. A small problem with an individual part, if left unchecked, can result in a costly system-wide failure. These contingencies not only impact building performance but can also reduce staff effectiveness and wellness.
A successful O&M policy should be baked into the building procurement and ownership process. It should be “lean” — as simple and straightforward as possible — and well-informed, with maintenance needs mitigated by careful design and construction. Here’s a roadmap to guide the process of developing and implementing a successful O&M policy, organized by project phase:
Phase 1: Project inception and estimation
- Projection and estimation of costs for proper building O&M.
- Assignment of an O&M representative to the process.
Phase 2: Programming
- Definition of service life expectations.
- Projection of efficiency targets for energy and water usage.
- Definition of commissioning and third-party oversight required during design and construction.
- Establishment of design standards and codes, including non-statutory standards if desirable.
- Adoption of ease-of-maintenance and risk-mitigation concepts at the design management level.
- Ease-of-maintenance means designing with the intent to facilitate maintenance tasks.
- Risk-mitigation means minimizing the risk of unexpected component and system failures as well as potential life-safety hazards.
- Allowance in the project budget and representation in the RFP for consultant services relating to the two above-mentioned concepts.
- Evaluation of RFP submissions to ensure consultants have adequately responded to these concepts in the assignment of experienced personnel.
- Preliminary outline of O&M plan, including division of maintenance requirements by the building owner or an approved O&M service provider.
Phase 3: Design Development
- Ensure O&M needs are properly represented in design review.
- Establish review procedures that assure implementation of ease-of-maintenance and risk-mitigation principles.
- Schedule timely waypoint reviews with the design team to avoid abortive work.
- Follow up on these reviews with checklists to ensure design execution of O&M considerations.
- Review owner’s current maintenance practices and recommend improvements from current industry best practices.
- Define a maintenance strategy including plans for conditions-based or corrective maintenance, scheduled maintenance, and proactive or reliability-oriented maintenance.
- Consider manufacturer/installer extended warranties for critical building systems including elevators, mechanical, and electrical systems.
Phase 4: Construction
- Ensure review procedures are in place to prevent revision or omission of maintenance measures.
- Avoid revision to selected materials or systems that change maintenance requirements resulting in greater maintenance needs or increased safety risks.
- Ensure that ease-of-maintenance and risk-mitigation principles are applied in situations where maintenance risks are identified in shop drawings or delegated design process.
- See that comprehensive inspection of work is carried out by properly qualified professionals, by the system manufacturers themselves, and through detailed checklists to verify adherence to maintenance specifications.
Phase 5: Close-out and Warranty Period
- Ensure close-out procedures, commissioning, and warranty period inspections are properly completed and signed by relevant agencies, consultants, and O&M service providers.
- Require that the O&M service provider is fully involved in the final stages before completion and during the warranty period.
Phase 6: Ongoing Operations
- Apply preventative, scheduled, and proactive maintenance instead of conditions-based or corrective maintenance.
- Ensure that the requirements and procedures of the maintenance plan are fully adhered to.
- Establish a review and approval protocol for the senior maintenance manager, including regular reporting to building management on the status of recently completed, ongoing, or anticipated maintenance. This must include a report of expenditures and estimated risk assessments for such work, noting any cost variances from projected allowances for future planning purposes.
- Ensure that where required in the maintenance plan or manual, properly qualified companies carry out maintenance work.
Some buildings get second acts, with major adaptations of use over their service life. This requires other procedures such as recommissioning, service life extension programs, and code compliance upgrades. The impact of such evolution on the O&M process is a subject for a future post.