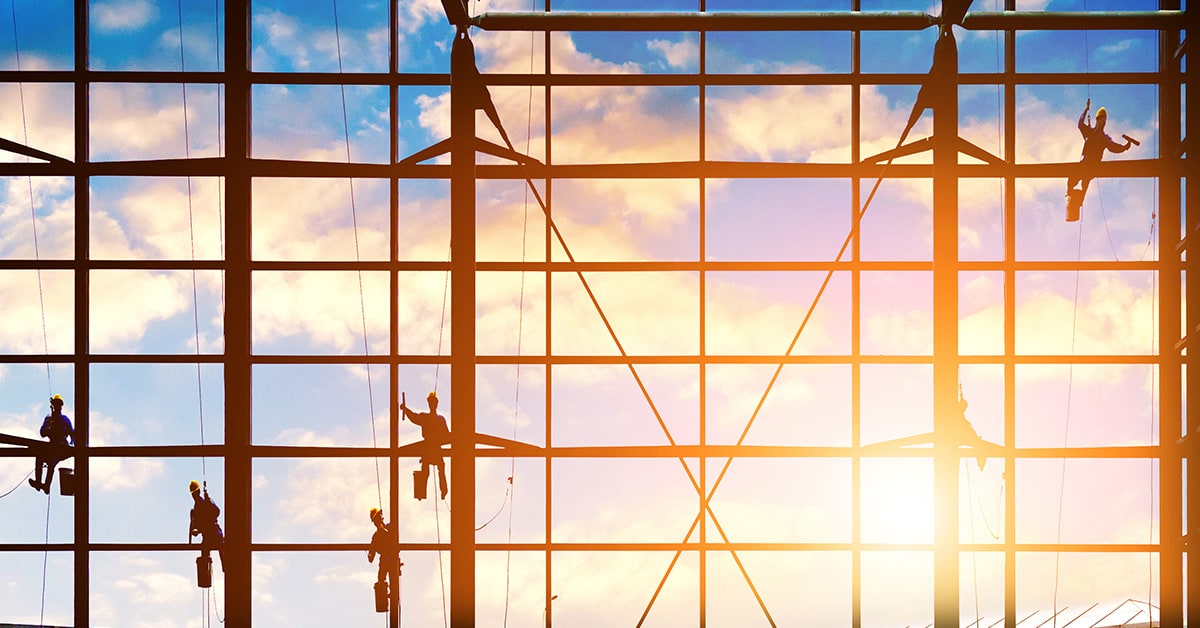
.
In our first post in this series, we made the case for comprehensive operations and maintenance planning. In part two, we delve deeper into O&M by identifying five principal objectives and three different approaches.
So you’re convinced: developing a comprehensive building operations and maintenance (O&M) plan is worth it [see our first post on O&M]. It’ll save costs in the long run, protecting both the physical assets and human resources of an organization. Now let’s take a step back. Let’s define the terms, the principal objectives, and some of the approaches that can lead to achieving those objectives.
First, for the record, let’s clarify the meaning of the terms: “Operations and Maintenance” refers to the combination of administrative and technical actions that ensure a building performs to acceptable and predictable standards, and does so continually for the duration of its intended service life. Operations encompasses the management and implementation of tasks associated with the day-to-day running and the building, while maintenance includes the further administration of those tasks necessary to maintain the building and ensure its intended performance to an optimal level.
If the overall goal of O&M is to ensure optimal building performance, this can be subdivided, for the sake of analysis and implementation, into five principal objectives:
- To extend the useful economic service life of a building.
- To minimize the risk of unplanned expenses.
- To satisfy lenders, insurers, or legal requirements to provide a safe, secure, healthy, and efficient environment for occupants and the public.
- To minimize the deterioration of assets.
- To preserve the aesthetic appearance of the building, which contributes to the owner’s corporate or organizational image.
With the objectives thus identified, there are multiple ways of pursuing and managing O&M, each associated with different costs and benefits. Three principal approaches should be considered during the design process and thereafter:
1. Conditions-based or corrective maintenance
Example: Don’t replace a chiller unit until it fails.
This a reactive approach to maintenance, carried out on an “as needed” basis. It is the most common, default form of maintenance. While it mirrors the old adage, “If it ain’t broke, don’t try to fix it,” it carries the highest potential risk of disruptive and detrimental failures. Unforeseen or predictable system failures can severely impact occupant comfort and safety, building performance, and asset value. Hint: a more robust O&M plan is advisable.
2. Scheduled and preventive maintenance
Example: Replace a chiller unit on a predetermined date, before it fails.
Most building systems carry manufacturer recommended inspection and maintenance plans, which define the various levels of maintenance, and the frequency by which they should be carried out. These will apply both during and after warranty periods. Typically, such scheduled maintenance must be carried out by a manufacturer or approved agent to maintain the validity of a system’s warranties. This approach may include preventive maintenance, in which parts of assemblies or entire systems are replaced proactively before they fail. These plans are based on manufacturer’s research into the service life of the system and its constituent parts. It considers the point at which component failure — and with it the associated risk to the wider system and the building itself — reaches a level of probability and risk deemed unacceptable by the manufacturer.
3. Reliability-oriented maintenance
Example: Monitor HVAC system to determine chiller replacement date.
Related more to mechanical and electrical systems, this entails the proactive or reactive monitoring and stabilization of systems to ensure optimal performance and reliability.
Building maintenance and operations should be part of every architect and building owner’s playbook. In our experience working with clients and consultants, it helps to start with a firm understanding of the objectives and the primary approaches of O&M. The end result is a more livable, high-performing, and economically viable building.
This is the second in a series of posts on building operations and maintenance.