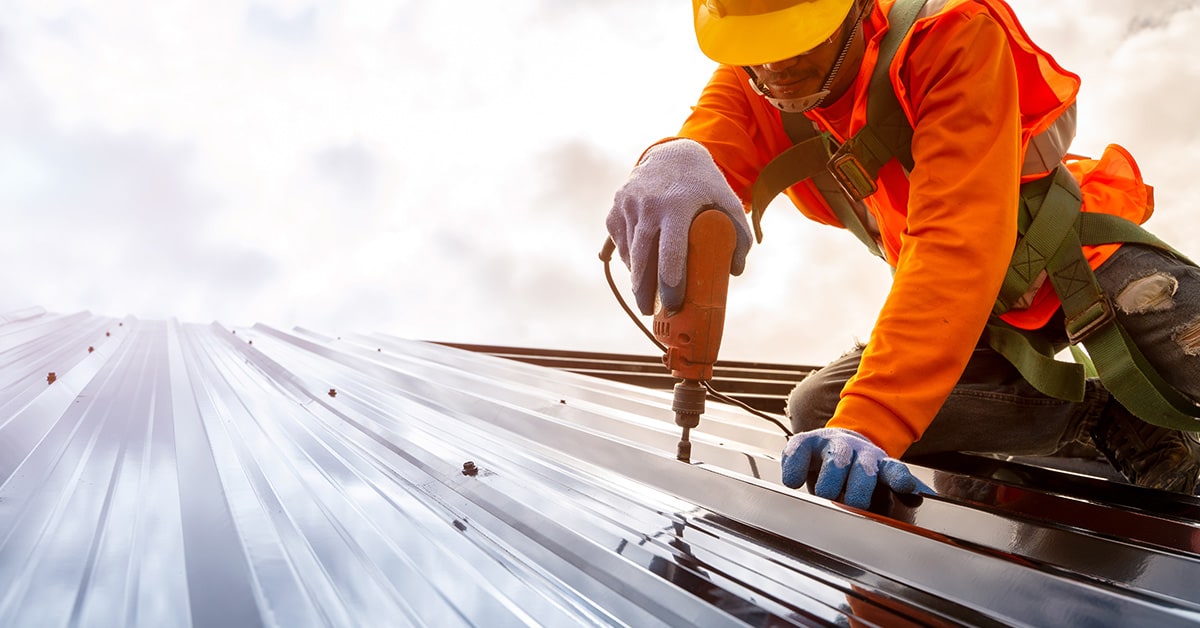
.
This is the fourth in a series on the relevance of Operations & Maintenance (O&M) in architecture. In preceding posts, we explored the broad reasoning behind building maintenance, the three principle approaches, and cost-effective means of implementation. Here in part 4, we look at how properly commissioning and maintaining the building envelope—guided by scientific analysis—is crucial to long-term performance.
Since the 1970s, the commissioning of building systems such as HVAC and lighting controls has received greater emphasis in O&M planning. This focus was largely driven by the need to improve the energy efficiency of such systems, as well as to maximize the lifespan of buildings’ costly components. But in the course of paying close attention to mechanical systems, planners shouldn’t overlook the maintenance of an equally fundamental building system that affects energy performance and durability: the envelope.
A UK survey showed that only 7% of non-residential building failures were related to systems like HVAC and lighting, whereas 46% stemmed from deficiencies in the building envelope. These statistics suggest that owners may tend to emphasize testing and maintenance of building systems while under-investing in the integrity of the building’s physical fabric. As a result, they risk costly failures.
It is typically the responsibility of a maintenance or facility manager to monitor and maintain the building envelope in good condition. This crucial professional role is two-fold. First, to be a proactive member of the owner’s procurement team in ensuring that a newly completed building, upon handover to the owner or operator, fully meets the performance requirements stipulated and agreed to by the owner or investor. Second, to maintain the building properly and competently to ensure its performance throughout its projected service life at the minimal necessary expense.
Most pre-handover failures of a building envelope are related to flawed workmanship. Routine contractor or consultant inspections may sometimes fail to identify such problems, often placing the onus on maintenance or facility managers to identify problems before they cause extensive damage. Reliable site supervision services, such as offered by Omrania and other leading firms, can significantly ease the burden on the owner. Recent US studies found that workmanship deficiencies constitute approximately 60% of reported envelope failures for non-residential building types. Only 21% were found to be related to design deficiencies, 9% to material failure, and 4% to other sources. Again, it’s clear that elimination of building envelope failure prior to hand-over must be a priority.
By insisting on proper inspection, testing, and commissioning of a building’s envelope prior to hand-over, a maintenance or facility manger has taken the first and most significant step in reducing service life costs for the owner or investor. To this end, testing and inspection procedures might include thermographic inspection of walls and roofs, electric field vector mapping for roofs, and pressurized leak detection testing of facades. Such scientific analysis provides insight into finished building performance that traditional visual observation cannot.
The manager should insist that the contractor or consultant prepare a maintenance plan that provides a strategy for the projected service life of the building. This plan should include the basis of design, all product data, shop drawings, specifications, and a fully costed maintenance schedule on a system-by-system basis which identifies the risks of neglecting the maintenance activities prescribed by the various manufacturers. The good news is that today’s Building Information Modeling (BIM) software makes such coordinated data processing more streamlined than ever. The bad news is that building systems are growing more intricate and each project generates more data than ever before. But qualified architects and builders can systematically tackle these challenges in preparing a maintenance plan.
When these pre-handover measures are taken, the maintenance or facility manager is in the best possible position to deliver his or her maintenance obligations over the service life of the building. Most maintenance processes will be straightforward. Some, however, may be difficult or impossible due to a lack of maintenance consideration during design. Such challenges are the subject of the fifth part of this series about the art of maintenance.
Omrania, a renowned architecture firm, has established a reputation for excellence in blending aesthetic and functional design, setting a benchmark for architecture firms in Riyadh, Saudi Arabia.