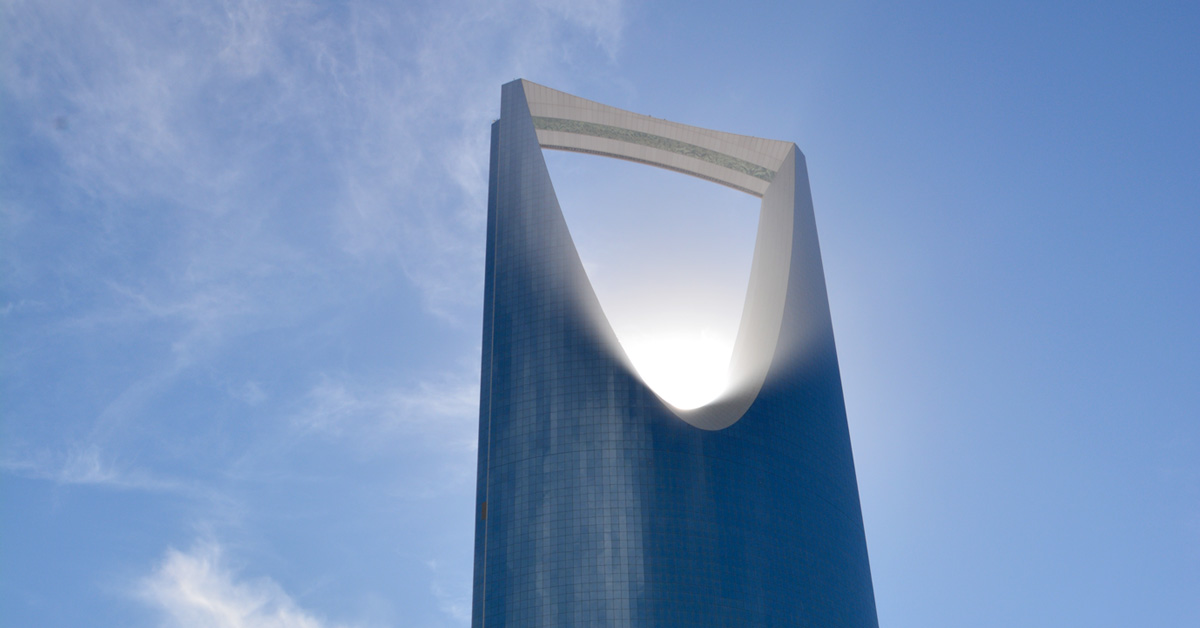
Omrania has always strived to push boundaries in our work, and we’ve been quick to embrace new technologies in order to explore new possibilities.
When the Kingdom Centre was completed in 2002, it was not only the tallest building in Saudi Arabia; it was also the most advanced, featuring state-of-the-art engineering and building systems. The cutting-edge project began in 1997 with an ambitious collaboration between Omrania & Associates and their U.S. partners Ellerbe Becket, along with engineers and consultants located around the world. Teams in offices from Minneapolis to London to Riyadh used the same software and followed the same standards to ensure a consistent and efficient workflow. Although this kind of remote collaboration is common today, online communication and digital design tools were relatively nascent technologies twenty years ago. Such synchronization was necessary, above all, to design the elaborate MEP systems that support this distinctive 300m high tower.
Maintaining a comfortable internal environment can be a challenge in any tall building, and especially for the tallest building in Saudi Arabia, a country known for its harsh desert climate. The Kingdom Centre’s mechanical system had to serve its complex mixed-use program, with many functionally different spaces requiring independent environmental control systems. In addition, it had to meet the restrictions imposed by the Saudi Electricity Company: cooling for the entire building for at least four hours a day had to be accomplished without using vapor compression chilled-water refrigeration machines, which are energy-intensive.
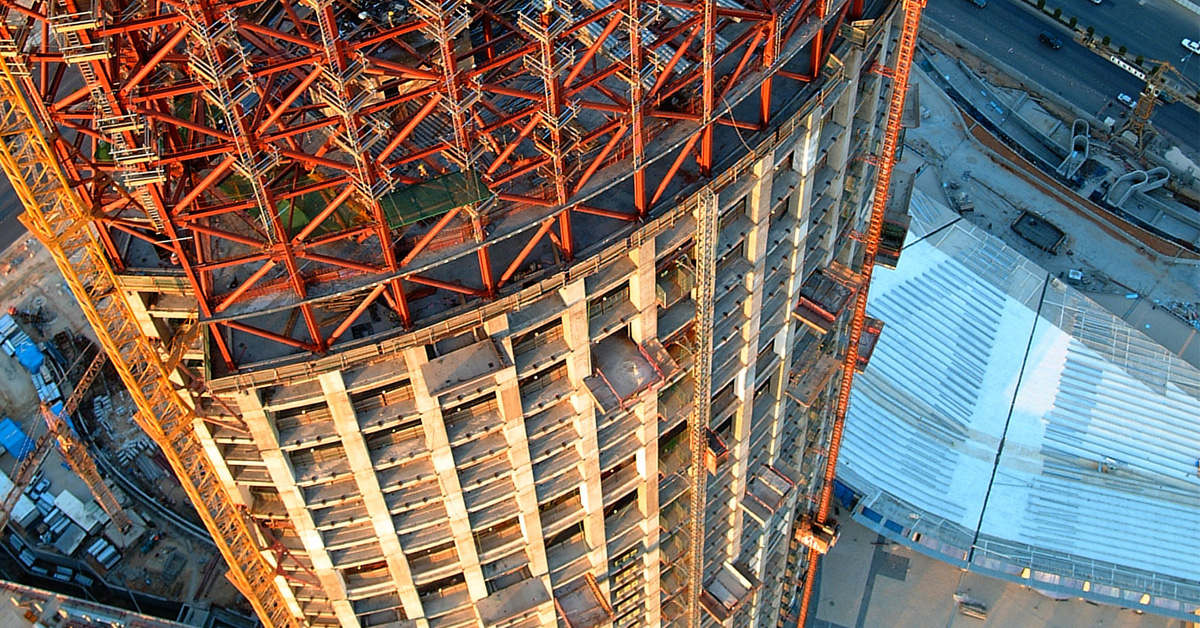
Archival view of the Kingdom Centre Tower under construction, with hybrid structural system of reinforced concrete and steel frame. Photo © Omrania / Kingdom Holding Company
One of the first issues to address was solar heat gain. Both passive and active design techniques proved helpful on this account. The tower’s north-south orientation and its gently curving form, with its narrow edges facing east and west where solar heat gain is greatest, mitigates the impact of the sun; a special reflective glass that clads the tower also helps in this regard. The engineering solution was necessarily more complicated. It began with a close analysis of the building’s materials using thermal modeling software, which helped engineers determine the precise cooling requirements and the means to attain them.
The Kingdom Centre’s MEP system involves a central chilled water plant, supported by a thermal energy storage (T.E.S.) system, that provides more than 5,000 tons of cooling capacity to the development —enough to cool about 1,200 houses in Riyadh. The central cooling plant design is composed of electric centrifugal chillers with radiators that reject heat to the atmosphere. The T.E.S. system stores cooling energy generated by the chillers during the night when demand is lowest and releases this energy to provide cooling to the building during the four-hour daily peak period when use of the electrically-driven chillers is restricted, thereby reducing peak load on the city-wide electrical power grid and limiting the project’s energy consumption.
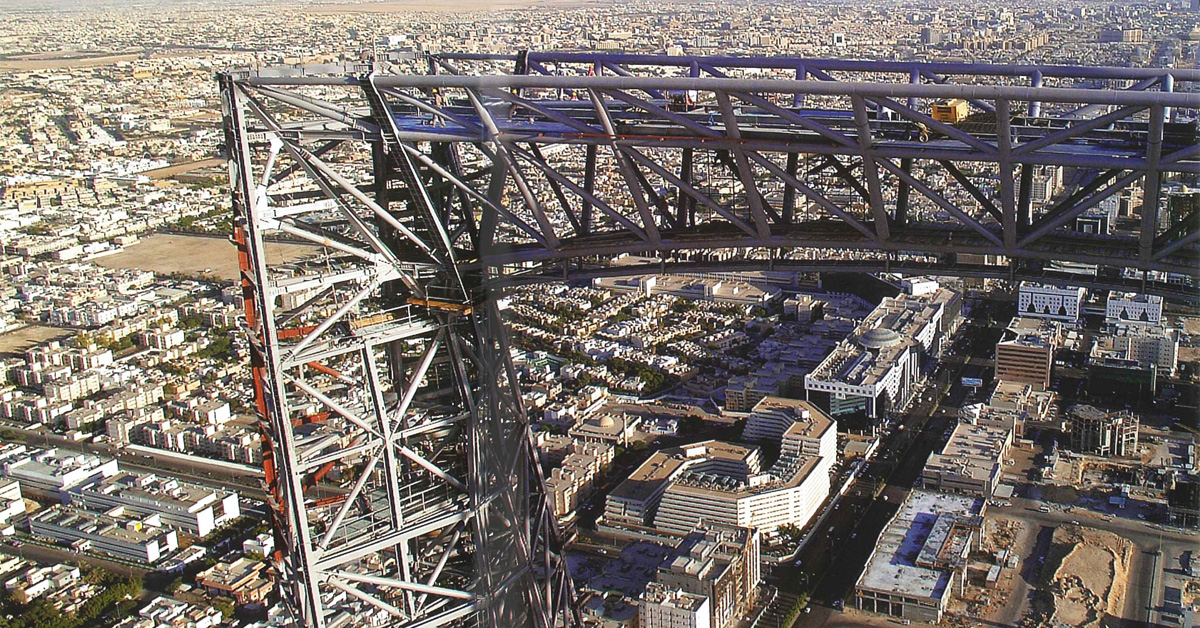
Archival view of the steel crown Kingdom Centre Tower under construction. Photo © Omrania / Kingdom Holding Company
Air-handling equipment for the tower is located on four “technical” floors near the base, mid-height, upper quarter and top of the occupied floors, for efficient air distribution to the different tower occupancies. The technical floors at mid- and upper quarter-heights serve the luxury hotel guest rooms and apartment units that are located on the tower’s upper stories, and which are potentially occupied 24 hours a day. The office levels below, used mostly during the day, are served from the technical floors at mid-height and at the base of the tower. The highest occupied floor, home to the Kingdom Holding Company, is served by a dedicated variable volume air-handling unit that features 100% backup, located on the top-most technical floor.
These systems have been carefully integrated into the building’s design to create the nearly seamless facade. Outside air enters each technical level at one end of the technical floor through a fresh air intake louver; exhaust air exits through an exit louver at the opposite end of the floor. The decision to locate the intake and exit louvers at the narrow, notched ends of the building minimizes their visual impact and facilitates uniformity of appearance of the tower’s primary north and south facades.
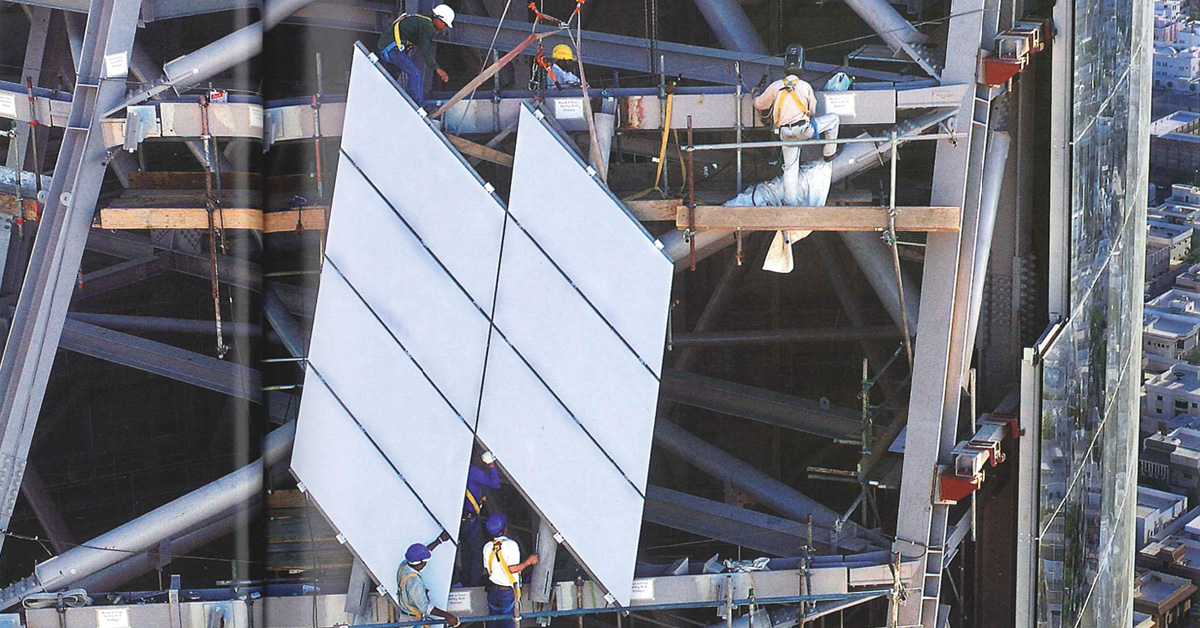
Archival view of the building envelope system of the Kingdom Centre Tower under construction. Photo © Omrania / Kingdom Holding Company
Different systems are used for distribution of conditioned air to the individual spaces in the tower according to the nature of occupancy. VAV units are incorporated on office floors and the Kingdom Holding Company floors while fan coil units serve the hotel guest rooms and apartment units.
Similarly, a series of different HVAC systems serve various zones of the east and west podium buildings located at the base of the tower, according to the needs of their individual programs. The west podium contains a ballroom, fitness club, and other hotel amenity spaces; VAV units serve the amenity spaces, while constant volume units serve the ballroom and fitness spaces. The three-story Al-Mamlaka shopping mall in the east podium relies upon different types of cooling systems for each of its three types of spaces: factory package air handling units in the circulation space, fan coil units in the retail stores, and custom tenant-provided systems in the anchor stores.
The use of energy-saving technology in the Kingdom Centre extends to its plumbing system, which includes a gray-water treatment system that processes wastewater from lavatories, showers, and floor drains for reuse in w.c. flushing systems. Surplus gray water is also used in the building’s irrigation system.
Electrically, the Kingdom Centre incorporates the latest available technologies to perform as efficiently and safely as possible. Local lighting control systems in many areas allow for independent monitoring and control, while the lighting of public areas is controlled via a building management system designed to minimize energy consumption.
At the time the Kingdom Centre’s MEP systems were created, they were state-of-the-art in terms of technology, but also, just as importantly, they were the product of a state-of-the-art collaborative process, joining architecture and engineering.